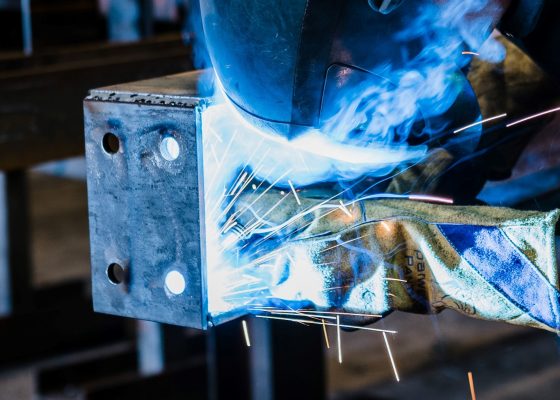
What is BS EN 1090?
- BS EN 1090 is the UK’s implementation of the European EN 1090 standard, the scope of which covers technical requirements for the fabrication and assembly of steel and aluminium structures in construction projects.
- BS EN 1090 has the same technical requirements of the European EN1090 standard, but different marking and enforcement mechanisms due to the UK’s exit from the European Union.
What is UKCA marking?
- UKCA (UK Conformity Assessed) marking is a new product marking that indicates conformity with the applicable requirements for products sold within Great Britain.
- The EN 1090 standard requires that structural steel and aluminium products sold in Europe must be CE marked. In the UK, following Brexit, it is the UKCA mark that is required to demonstrate compliance with the standard.
Who is this standard for?
BS EN 1090 will be used by the fabrication and manufacturing industries, especially those with critical safety requirements. It is relevant to:
- Manufacturers of structural steel
- Structural engineering services
- Anyone involved in construction work that requires steel or metal components as part of the building.
Why is it BS EN 1090 and UKCA marking important for structural steel?
- It is a legal requirement, compliance with the standard is mandatory (click here).
- It ensures the safety and compliance of products through rigorous manufacturing requirements and conformity assessment, offering customer reassurance for the integrity of their structural steelwork (click here).
What are the requirements of BS EN 1090?
Below is an overview of some requirements of BS EN 1090, and how it relates to us, Westcountry Fabrication Ltd (WCF), as a steel fabrication company. Westcountry Fabrication Ltd celebrate another year of certification and compliance with BS EN1090 following the audit of our systems by SCCS (Steel Construction Certification Scheme) and are proud to display the UKCA mark alongside our fabricated structural steel work.
EN 1090-1
- Specifies the requirements for assessing and verifying the conformity of structural steel and aluminium components
EN 1090-2
- Details the technical requirements for the execution of steel structures, including requirements for welding procedures, welder qualifications, cut edge quality, and hot/ cold forming.
EN 1090-3
- Details the technical requirements for the execution of aluminium structures
Factory Production control (FPC)
- Manufacturers must implement a Factory Production Control system to ensure consistent product quality and compliance with the standard. WCF have a detailed Factory Production Control system in place which covers aspects including ‘Welding Quality Management System’, ‘Calibration and Maintenance', and ‘Verification of Purchased Product’.
Welding Procedure Qualification
- Welding Procedures must be specified and tested in line with relevant specifications. Both BS EN ISO 15613 and BS EN ISO 15614 are referenced in BS EN1090 for the execution of steel and aluminium structures and are the standards for which welding procedures are tested. For example, WCF has a WPQR (Weld Procedure Qualification Record) for all welding procedures used in production such as single run fillet welds of box to plate. These procedures are recorded and tested by an independent UKAS accredited body via Code a Weld.
Welder Qualification Test
- BS EN 1090 mandates the use of qualified welders as part of the overall Factory Production Control system required for CE (Europe) or UKCA (in the UK) marking. BS EN 1090 requires that welders performing work under these standards must be qualified in accordance with BS EN ISO 9606-1 for steel and BS EN ISO9606-2 for aluminium. WCF welders and fabricators are independently assessed and tested periodically to ensure that their performance complies with the required standard. Code a Weld complete surveillance audits for WCF and test pieces are sent to an independent UKAS accredited laboratory.
Responsible Welding Coordinator
- Under BS EN 1090 companies performing welding work in execution classes EXC 2, EXC 3 and EXC 4 are required to have access to a Responsible Welding Coordinator (RWC) to manage the welding processes. The RWC’s responsibilities include reviewing contracts, overseeing welding procedures and welder qualifications, verifying materials, and inspecting welds to meet quality requirements. Our RWC at WCF is Jack Gailer, Managing Director, who has over 20 years of welding experience, as well as having undergone specific training and certification for the role of RWC.
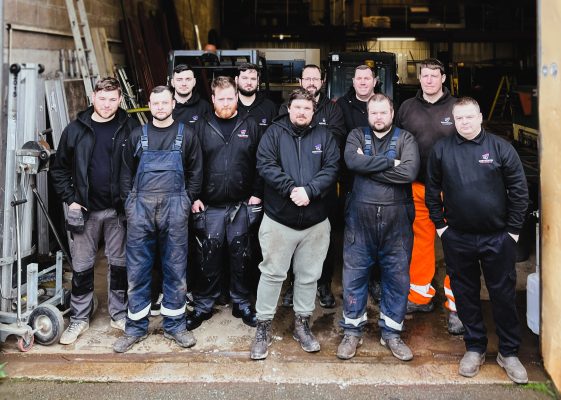
Traceability of material
- WCF source steel from accredited suppliers. Comprehensive documentation and traceability of materials, processes and test results are required as part of the FPC system to demonstrate compliance with the technical requirements of BS EN1090 for steel structures. For WCF this means for every item of steel we receive, a test and inspection certificate is issued which states that the steel has been inspected in relation to the relevant standard for the product.
Execution Classes (EXC)
- The standard specifies four execution classes (EXC1, EXC2, EXC3 and EXC4) based on the potential risk to public safety if the component or structure fails. Designers must identify the appropriate execution class. WCF are certified to EXC2 which covers most building structures in the UK, see here for more detail.
Summary
BS EN 1090 is a mandatory standard that applies to manufactured steel products and components. Compliance with this standard requires monitoring and testing of materials, products and of welders skills to ensure compliance. Westcountry Fabrication are committed to ensuring compliance with the required standard through ongoing monitoring and assessment, the result of which enables us to UKCA mark our products. It is important for designers, engineers, builders and fabricators to be familiar with the standard to ensure safety, compliance and conformity of products and ultimately installations.